Don’t turn away that skylight case just yet
A skylight often constitutes a dangerous condition; here’s how to prove it
You get a call from the family of a worker who fell through a skylight and died. They want you to pursue a wrongful- death case. Although premises-liability cases can be extremely difficult, if you get the right documents and testimony, you just might be able to obtain compensation for the family, while improving the safety of premises for others in the future. So, before you decide to pass on that challenging skylight case, consider the important factors below.
A serious health and safety issue
Workers fall through skylights and floor openings so often that the Centers for Disease Control through the National Institute for Occupational Safety and Health (NIOSH) has issued “Alerts” to building owners, skylight manufacturers and others seeking their assistance in preventing these falls. (Centers for Disease Control (“CDC”), Workplace Safety & Health Topics, Fall Injuries Prevention in the Workplace, available at http://www.cdc.gov/ niosh/topics/falls); NIOSH, Alert, Preventing Falls of Workers Through Skylights and Roof and Floor Openings, Aug. 2004, p.1; DHHS (NIOSH) Publication No.: 2004-156; available at http://www.cdc.gov/ niosh/docs/2004-156/); and NIOSH, Alert, Preventing Worker Deaths and Injuries from Falls Through Skylights and Roof Openings, Dec. 1989, DHHS (NIOSH) Publication No. 90-100; available at http:// www.cdc.gov/niosh/docs/1989-100/). Falls are a common hazard found in all types of occupational settings. (CDC, Workplace Safety & Health Topics, Fall Injuries Prevention in the Workplace, available at http://www.cdc.gov/niosh/topics/ falls.)
The highest frequency of fatalities due to falls is experienced in the construction industry, where fall incidents are often associated with unstable surfaces, floor holes and roof openings (such as skylights). (Ibid.) Injuries due to falls cause a considerable financial burden with medical costs and worker’s compensation estimated at more than $70 billion a year in the U.S. (Ibid.)
Studies show that employers, workers and building owners do not fully appreciate or recognize the fall hazards and dangers of working near skylights. (NIOSH, Alert, Preventing Falls of Workers through Skylights and Roof and Floor Openings, Aug. 2004, p.1; DHHS (NIOSH) Publication No.: 2004-156; available at: http://www.cdc.gov/niosh/ docs/2004-156/.) A family who has lost a loved one due to a fall through a skylight, however, will understand the danger, and will express horror that a simple safety screen or guardrail was not used. After all, safety screens and guardrails are available for skylights of all shapes and sizes at relatively low cost. A quick Internet search provides numerous safety options and the pricing for many of them. (See, http://garlocksafety.com/images/products/GarlockSafetyBrochure-web.pdf, p. 2, showing cage guards, safety screens and other options to prevent falls through skylights; see also, http://safetyrailsource.com/Skylight_Rails_and_Screens/skylight_rails_and_screens_model_selection_sheet.htm) (with numerous skylight safety options); and Grainger.com which has numerous skylight protective devices for $388 and up, (available at: http://www.grainger.com/category/skylight-guards/fall-protection/safety/ecatalog/N-o8c?redirect=skylight+guards.)
Energy efficiency and cost-savings
We have all seen skylights on the roofs of buildings and perhaps even on our own homes or offices. Skylights are a great way of allowing natural light into a building and providing significant savings in energy costs to the building owners and/or tenants. There are a wide variety of skylights, including sizes, strengths, shapes, and materials from which they are made. The size, strength and location of skylights will be important considerations in analyzing your potential case.
More skylights will be used in the future
California is recognized as a leader in energy-efficiency, including in its energy efficiency standards for buildings set forth in California’s Code of Regulations (CCR), Title 24. (California Energy Commission, available at http://www.energy.ca.gov/title24/2013standards/rulemaking/ and http://www.energy.ca.gov/title24/.) California’s Energy Commission boasts savings to Californians of over $74 billion in reduced electric bills since 1977 due to California’s energy efficiency standards and regulations which not only conserve electricity and natural gas, but also prevent the need to build more power plants.
In 2014, California tightened its energy standards for new construction which will result in the use of even more skylights on buildings as well as retrofitting existing buildings with energy efficient products, such as skylights. The goals of energy efficiency and sustainability are commendable and important for California, but equally important is the safety of these buildings and skylights.
Rules, regulations and building codes
Buildings in the United States are regulated by Building Codes which provide minimum standards to safeguard the property and public welfare by controlling the design, construction and quality of materials for buildings and structures. Skylights are considered structural components of buildings and are therefore, subject to various loads, forces and weights. Because commercial and industrial skylights are mostly installed on flat roofs and will be exposed to live loads like rain and snow, various Building Codes and Regulations mandate the loading requirements for skylights.
Retaining a qualified expert
In order to determine the building codes, regulations and rules applicable to the premises where your skylight incident occurred, you should retain the services of a qualified expert. Typically, a safety engineer will be most useful because of their expertise in identifying, eliminating and controlling hazards. You should obtain the architect’s plans and drawings to determine which Building Codes and regulations applied to the premises where your client was injured. Your expert will then assist in determining what is stated in the particular year’s Building Codes and regulations about skylights as well as overall roof-loading requirements. For example, portions of the 2007 California Building Code specify that all roof surfaces subject to maintenance workers, [be able to withstand] 300 lbs. concentrated load. (Cal. Bldg. Code (2007), Structural Design 1607.11, p. 14, and Table 1607.1, p. 11.)
OSHA considers a skylight a “roof opening”
Skylights must comply with both Federal and State OSHA Regulations. In February of 1984 an OSHA Interpretation Letter established that skylights are “an opening in the roof of a building through which persons may fall.” (OSHA Interpretation Letter, Feb. 16, 1984, Dept. of Labor, available at https://www.osha.gov/pls/oshaweb/owadisp.show_document?p_table=INTERPRETATIONS&p_id=19180.)
OSHA’s Interpretation Letter required “that skylights in the roof of buildings through which persons may fall while walking or working shall be guarded by a standard skylight screen or a fixed standard railing on all exposed sides.” (Ibid.)
OSHA’s Letter further provided: “When a skylight screen is selected for safeguarding the opening, and in the event the skylight is constructed of plastic material subject to fracture (as glass would be), then the skylight must be at a minimum be provided with a skylight screen capable of withstanding a load of at least 200 pounds applied perpendicularly at any one area of the screen.” (Ibid.)
California’s Code of Regulations
In California, the Code of Regulations, Title 8-Industrial Relations, Chapter 4-Division of Industrial Safety, Subchapter 7-General Industry Safety Orders, 2008 (CCR T8 GISO) sets forth the safety requirements for skylights. Section 3212-Floor Openings, Floor Holes, Skylights and Roofs (CCR T8 GISO) establishes that roof openings (including skylights) should be guarded: “(a)(1) Every floor and roof opening shall be guarded by a cover, a guardrail, or equivalent on all open sides...” (Cal. Dept. of Industrial Relations, CCR, Title 8, Chap. 4(c), section 3212, available at (http://www.dir.ca.gov/title8/3212.html.))
Section 3212(b) explains the loading requirements for a cover: “Floor and roof opening covers shall be designed by a qualified person and be capable of safely supporting the greater of 400 pounds or twice the weight of the employees, equipment and materials that may be imposed on any one square foot area of the cover at any time...” (Ibid.)
Section 3212(e) further sets forth protection to prevent falls through skylights: “Any employee approaching within 6 feet of any skylight shall be protected from falling through the skylight or skylight opening by any one of the following methods:” . . . “Skylight screens. The design, construction, and installation of skylight screens shall meet the strength requirements equivalent to that of covers specified in subsection (b) above...” “Guardrails meeting the requirements of Section 3209...” “Covers meeting the requirements of subsection (b) installed over the skylights...” (Ibid.)
California’s Code of Regulations, Title 8, Subchapter 4, Construction Safety Orders also describes the requirements of guarding skylight openings. Article 19-Floor, Roof and Wall Openings, Section 1632(b). Floor, Roof and Wall Openings to be Guarded, states: “(b)(1) Floor, roof and skylight openings shall be guarded by a standard railing railings and toeboards or cover.” (Cal. Dept. of Industrial Relations, CCR, Title 8, Chap. 4, art. 19, section 1632(b), available at (http://www.dir.ca.gov/title8/1632.html.)) Section 1632(b)(1) then goes on to explain the requirements for the skylight cover loading: “Covers shall be capable of safely supporting the greater of 400-pounds or twice the weight of employees, equipment and materials that may be imposed on one square foot area of the cover at any time...” (Ibid.)
Guardrails and screens
Federal OSHA Regulations also address guarding against fall hazards posed by skylights. OSHA General Industry Standard 29 CFR 1910.23(a)(4) requires, “every skylight floor opening and hole shall be guarded by a standard skylight screen or a fixed standard railing on all exposed sides.” (Dept. of Labor, OSHA, 29 CFR 1910.23(a)(4); available at https://www.osha.gov/pls/oshaweb/owadisp.show_document?p_table=STANDARDS&p_id=9715.) The Federal OSHA Construction Standards also require guardrails for skylights. (Dept. of Labor, OSHA, 29 CFR 1926.501(b)(4)(i).)
Certainly, the best and safest option to prevent deaths, injuries and falls is for the building owner and/or entity controlling the roof, to place the recommended safety equipment (i.e., screens, guardrails and covers) over the skylights. But, these pieces of safety equipment are rarely used despite their obvious life-saving benefits.
Architects’ plans and drawings
Architects often design buildings with many skylights. Commonly, the architect will call out the brand, size and model of the skylight to use in the architectural plans and drawings. A general contractor will then order the skylights and hire an installer to install them. The architect’s plans and design drawings should be carefully reviewed and analyzed. Architect’s design drawings and plans will often contain “Safety Notes” and “General Notes” recommending that the owner, contractor and/or entity in control of access to the premises provide safety equipment for the skylights, including guardrails and warnings. The following language might be included in the Safety Notes, in all-caps and bold font: “This architect recommends the use of guardrails…if guardrails are not used the owner shall accept full responsibility. In addition, the contractor shall provide clearly legible signs at these locations stating ‘Caution: No Guardrail.’” These architect’s notes could constitute notice that the unguarded skylights are a dangerous condition. Make sure you inquire of the owner, contractor and all others reviewing, relying upon and/or “signing off on” the plans and drawings whether they carefully reviewed them, approved of them, read and agreed with them.
You should attempt to determine why guardrails, screens and/or other protective devices were not used with the skylights and whether they were considered at some point. You will likely find that the safety equipment was not used because “no one else uses it,” it’s not standard practice, or that it costs too much. However, even a cursory review of OSHA Regulations and California’s Code of Regulations, shows that this protective equipment is required and should be used.
Skylight manufacturers provide on-product labels cautioning building owners and designers
Skylights will often come with a label affixed to them with information such as:
This skylight is designed to withstand normal elements of the weather. It is not designed to withstand human impact or falling objects. This skylight should not be walked upon under any circumstances. The owner or designer should restrict access only to authorized personnel who have been adequately cautioned as to the location of the skylights and informed of the warnings above, or said owner should provide protective guardrails or screens around the skylights.
By providing this information, the skylight manufacturer is attempting to make known to the owner of the building, the contractor, and the architect, that the skylight (in the example above) cannot support an impact from a human and, therefore, should be guarded and/or access to the skylight should be restricted to those who have been cautioned about the skylights. The contractor, architect and owner are on notice that an unguarded skylight is a dangerous condition and/or hazard.
The National Institute of Occupational Safety and Health recommendations
The Centers for Disease Control through the National Institute of Occupational Safety and Health has provided the following recommendations/ instructions to building owners “to protect workers from falls through skylights:”
• Provide workers with printed documents showing the exact location of all skylights on the roof where they will be working . . . .
• Install permanent, suitable anchorage points for PFAS [personal fall arrest systems] on both new and existing buildings. Clearly mark their locations for workers.
• Install permanent railings around skylights or protective screens over individual skylights to protect workers or others who must be on the roof.
• Post warning signs on skylights and at entries (doors, stairs, ladders, or roof hatches) to areas containing skylights.
Post . . . signs in English and in the predominant language of workers who do not read English. . . .
If workers cannot read posted warning signs, warn them verbally. Use an interpreter if necessary.
• Place locks on all doors leading to roof-tops with skylights and provide keys to authorized personnel only . . .
NIOSH recommends a warning similar to the above be used and placed on the skylight.
In discovery, find out whether your building owner did any of the above to prevent injuries and death on their property. If they followed none of these recommendations, find out why. Was there only one entryway or access point onto the roof? Who was allowed to access the roof? Was there signage including adequate “Warning” language and pictograms to notify those entering the roof of the skylights and showing the dangers of falling onto skylights? Were there appropriate locations for those entering onto the roof to use safety equipment (such as lanyards and OSHA approved anchors/tie-offs if they were working on equipment near skylights)?
The photograph below shows why guardrails and screens are truly the only safe option. A 43-year-old worker assigned to clear snow from the roof, could not see through the snow, stepped on a skylight covered by the snow, and fell through it to his death.
(NIOSH, Alert, Preventing Falls of Workers through Skylights and Roof and Floor Openings, Aug. 2004, p.1; DHHS (NIOSH) Publication No.: 2004-156, available at http://www.cdc.gov/niosh/docs/2004-156/.)
NIOSH has also provided recommendations and requests to those manufacturing skylights to assist in improving safety and reducing injuries and deaths. (Ibid.) NIOSH investigation found that its own engineers estimated that a 200 pound person falling against a skylight could transmit 400-500 pounds of force against the skylight. (Ibid.) Therefore, any requirement that a skylight only be capable of handling loads of 200-400 pounds is inadequate. Premises owners should purchase stronger skylights and/or skylights with a metal grid or screen as an integral part of the skylight fixture. (See generally, Id.) Further, skylight manufacturers should indicate how long skylights and screens can be expected to maintain load capacity. Finally, conspicuous, clear signs and warnings should be used on the products themselves which comply with ANSI and OSHA standards.
In discovery, find out what the manufacturer provided the purchaser and/or building owner regarding cleaning and maintaining the skylight as well as the life expectancy of the skylight. If the owner and/or property manager failed to properly maintain and care for the skylights, thus causing them to be brittle and more likely to break upon impact, this is useful information in your premises case. Find out if there were other skylights that were cracked, leaking, broken, and/or in need of being replaced. You will need to obtain contracts and agreements between the various entities to determine who was responsible for the property, including rooftop equipment and skylights as well as agreements setting forth the schedule for replacement and/or repair of skylights.
Foreseeability of harm
Anyone coming near to an unguarded skylight could be in danger, especially due to slips, trips and falls. The Bureau of Labor Statistics’ Census of Fatal Occupational Injuries reported that “[a] preliminary total of 4,405 fatal work injuries were recorded in the United States in 2013”. (U.S. Bureau of Labor Statistics, Sept. 11, 2014, Press Release, available at http://www.bls.gov/news.release/ cfoi.nr0.htm.) Of those, “[f]atal falls, slips, or trips took the lives of 699 workers in 2013. (Ibid.) Fifteen percent of the fatal work injuries in 2013 resulted from falls, slips and trips, making it highly foreseeable that a worker will slip, trip and/or fall onto an unguarded skylight. (Ibid.)
During construction, falls are even more likely to occur. The U.S. Dept. of Labor, Occupational Safety and Health Administration (“OSHA”) warns that “FALLS ARE THE LEADING CAUSE OF DEATH IN CONSTRUCTION. In 2013, there were 294 fall fatalities (284 falls to lower level) out of 796 total fatalities in construction.” (U.S. Dept. of Labor, OSHA at https://www.osha.gov/stopfalls/ index.html.) OSHA believes “[t]hese deaths are preventable” and provides safety measures and regulations to reduce these injuries. (Ibid.) Unfortunately, the burden for safety is often placed on the employee/worker rather than the owner of the building, or those in charge of the overall operations at the premises.
Independent contractors and their employees are most at risk
Building owners and occupiers are, or should be, much more aware of the condition of their building/premises than independent contractors and/or their employees who come onto the premises for short duration and without understanding the layout, locations and load capacity of skylights and equipment at the premises. Between 2011 and 2013, the number of deaths to contractors in California due to skylights has risen. (Bureau of Labor Statistics, Fatal Occupational Injuries Incurred by Contractors 2011-2013; available online at http://www.bls.gov/iif/oshwc/cfoi/contractor.pdf.) Workers who come to the premises for a short and limited project, such as HVAC repairmen or roofers, are likely at the greatest risk, especially if they must work in close proximity to unguarded skylights.
Conduct an inspection with your expert
You will want to conduct an inspection with your expert as soon as possible to document everything at the premises in the condition it was in at the time of the incident. Ensure the skylight and all the pieces are preserved. You may want to conduct a Google Earth view of the building where the incident occurred to assist you in determining the number of skylights at the premises, as well as those in close proximity to mechanical equipment before you go. At the inspection, make sure you understand how the worker accessed the roof, how he positioned himself to conduct his work and how much movement was required to conduct the work. Also look for appropriate tie-off locations.
Was the skylight a dangerous condition?
Make sure your expert can testify that the skylight through which the worker fell constituted a dangerous condition and/or hazard. If the skylight was unguarded, was in close proximity to equipment upon which the worker was working, and did not support his weight upon impact, after a foreseeable fall, then it was likely a dangerous condition. Workers will often need materials to work on mechanical equipment, including hoses, wires, and tools, all of which could create additional foreseeable tripping hazards.
(NIOSH, Alert on Skylights, Dec. 1989, Summary Sheet, available at http://www.cdc.gov/niosh/docs/90-100/pdfs/90-100sum.pdf.)
Proving liability
California Jury Instructions 1000 et seq. set forth what you must prove to be victorious in your premises case. Essentially, owners, lessees, occupiers or those in control of the property must use reasonable care to keep the premises in a reasonably safe condition and “repair, replace, or give adequate warning of anything that could be reasonably expected to harm others.” [CACI 1000 and 1001].
If your decedent was an employee of an independent contractor on a construction project, the case may now be even more difficult against some defendants given the Privette v. Superior Court (1993) 5 Cal.4th 689, Toland v. Sunland Housing Group, (1998) 18 Cal.4th 253 and Seabright Ins. v. U.S. Airways (2011) 52 Cal.4th 590 decisions. These cases limit plaintiff’s ability to sue the hirer, even for failing to comply with statutory or regulatory safety requirements. You must now be able to prove direct and affirmative conduct and show that defendant negligently exercised its retained control over safety conditions which caused Plaintiff harm (CACI 1009B).
However, liability is not impossible.
Hooker v. Dept. of Transportation
A landowner/general contractor/subcontractor who retains control over safety procedures on a construction site is liable for its own actions that affirmatively contribute to the cause of injury to the employee of a subcontractor. Furthermore, the “affirmative contribution” can be an “act of omission”. (Hooker v. Dept. of Transportation (2002) 27 Cal.4th 198; Barclay v. Jesse M. Lange Distributor, Inc. (2005) 129 Cal.App.4th 281, 295; Kinsman vs Unocal (2005) 37 Cal.4th 659; Evard v. Southern California Edison (2007) 153 Cal.App.4th 137, 147.)
Imposing tort liability on a hirer of an independent contractor when the hirer’s conduct has affirmatively contributed to the injuries of the contractor’s employee is consistent with the rationale of our decisions in Privette, Toland, and Camargo because the liability of the hirer in such a case is not “‘in essence ‘vicarious’ or ‘derivative’ in the sense that it derives from the ‘act or omission’ of the hired contractor” [citations]. To the contrary, the liability of the hirer in such a case is direct in a much stronger sense of that term.
(Hooker, supra, 27 Cal.4th at 212.)
There will be times when a hirer will be liable for its omissions. For example, if the hirer promises to undertake a particular safety measure, then the hirer’s negligent failure to do so should result in liability if such negligence leads to an employee injury.
(Hooker, supra, 27 Cal.4th at 212, footnote 3.)
To find affirmative contribution, you must obtain each and every record, contract, and agreement setting forth the roles, responsibilities, duties and obligations of the parties involved. The records involving who was to do the work, how it was to be performed and who would be directing it, and overseeing it, are essential. Obtain the Corporate Safety Policies, Illness & Injury Prevention Program, Code of Safe Practices, Safety Manuals, Safety Meetings Minutes, Safety Practices, Job Hazard Analysis Form/ Checklist, Site Specific Safety Plan, Surveys and any and all Inspection Timelines, Checklists, Lease Agreements, Cal OSHA 300 Logs (for reportable illnesses and injuries), etc. A review of the United States Dept. of Labor, Occupational Safety & Health Administration, Data & Statistics, Establishment Search (available at https://www.osha.gov/oshstats/index.html) will allow you to search each entity involved, and see open investigations, citations, inspections, etc. This should assist you in preparing your discovery and depositions.
Also critical in a construction setting is obtaining information regarding who provided access to the building, what were “common work areas”, and who was responsible for those. Determine whether the worksite was a multi-employer worksite which may affect your liability analysis. Obtain any OSHA report prepared from the incident and carefully review the witness statements, photographs and citations issued.
Conclusion
Tackling a skylight case is no small task. But, with hard work, a qualified expert, and thorough discovery, you will hopefully be successful in your premises case, obtain compensation for the victim’s family, and promote safer buildings and workplaces.
Michelle M. West
Michelle M. West is an attorney with Robinson Calcagnie Robinson Shapiro Davis, Inc. in Newport Beach, CA where she focuses on catastrophic personal injury and wrongful death cases. She graduated Pepperdine University School of Law in 2003 and has practiced for over 10 years almost exclusively on behalf of injured individuals and consumers. Ms. West is a member of CAOC, CAALA, WLALA, Orange County Bar Association, and the OCBA Administration of Justice Committee. Ms. West was selected as a 2010 and 2011 SuperLawyer Rising Star in Southern California and in 2014 became a Fellow of the ABOTA National Trial College.
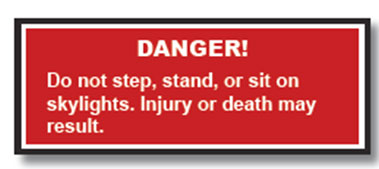
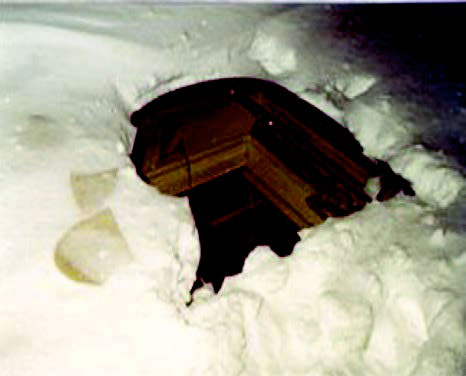
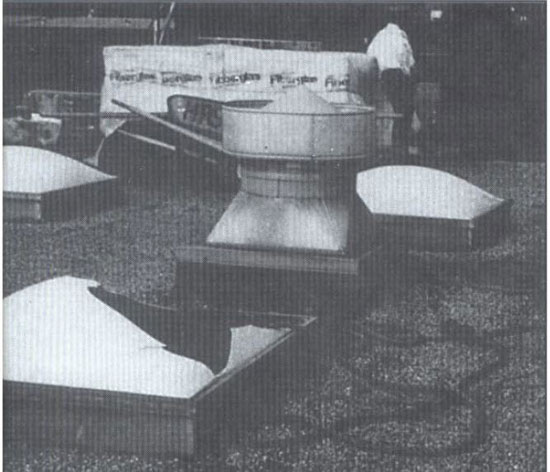
Copyright ©
2025
by the author.
For reprint permission, contact the publisher: Advocate Magazine